Labor is a core part of any construction project. It’s also one of its more significant expenses.
According to the U.S. Bureau of Labor Statistics, the mean average hourly rate for construction laborers in 2023 was $23.69. Multiply this by the number of employees you have and you’re paying hundreds of dollars an hour in labor costs.
That’s a whole lot. And if you can’t manage labor costs properly — whether it’s due to poor time tracking, inefficient scheduling, or high turnover— it can eat away at profits and impact your ability to stay competitive in the construction industry. That’s not something anybody would want.
In this guide, we’ll explore smart strategies to cut labor costs without compromising on quality or compliance. Some of them I’ve had to learn the hard way during my first few years in construction.
This Article Covers
- What are Labor Costs in Construction?
- Key Construction Labor Laws That Affect Labor Cost
- How Can You Legally Lower Construction Labor Costs?
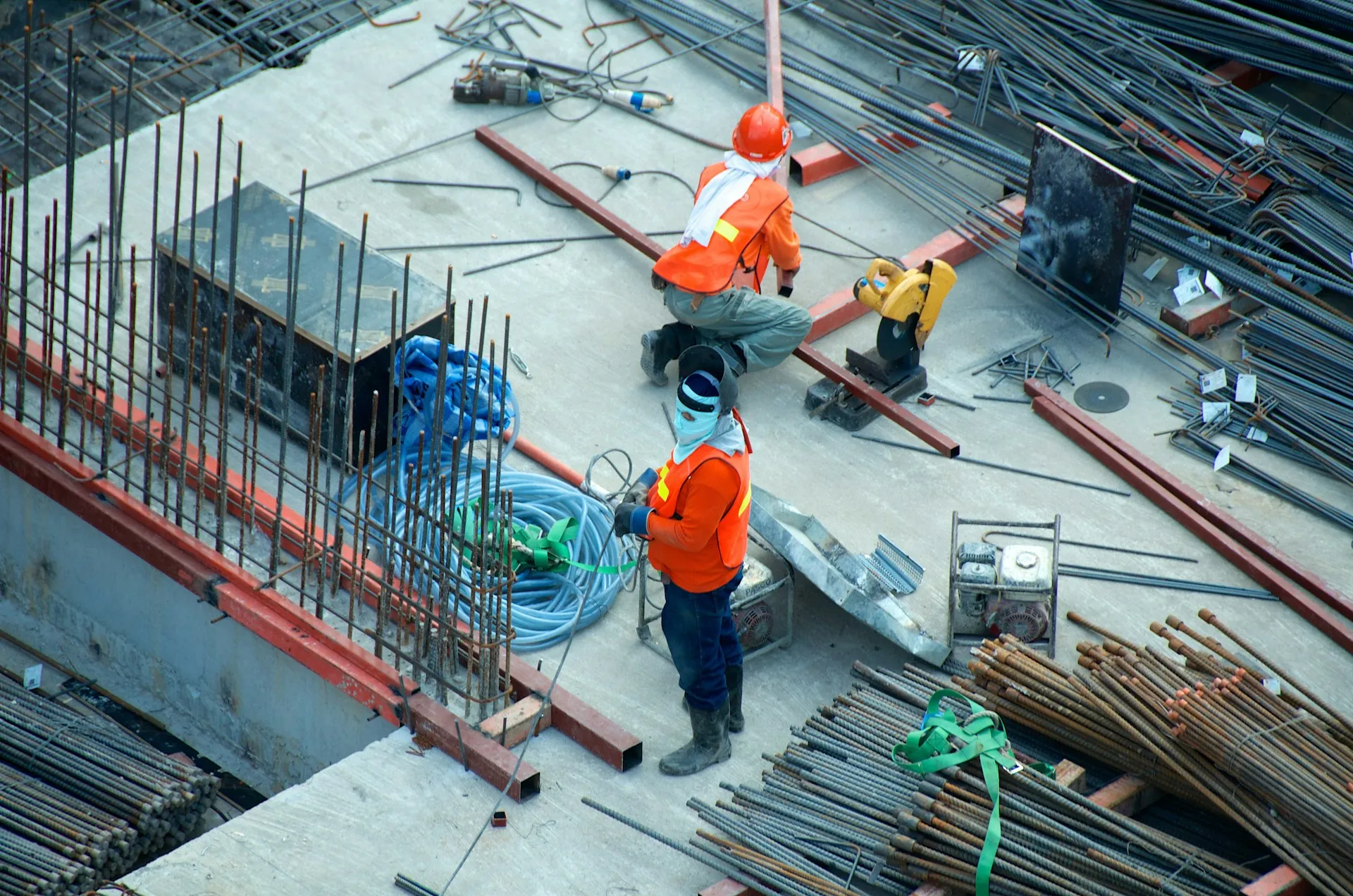
Photo by Etienne Girardet on Unsplash
What are Labor Costs in Construction?
Labor costs in construction refer to all the expenses related to the workforce involved in a project. This includes wages, overtime pay, benefits like health insurance, and bonuses given to both workers on-site and management staff overseeing the project.
Beyond direct wages, there are indirect labor costs that construction businesses should also consider. These include things like:
- Recruitment and training expenses
- Payroll taxes
- Equipment costs like company vehicles and phones
- Costs associated with safety and quality assurance, and so on
Factoring in these indirect costs is essential to get a complete picture of labor expenses.
Key Construction Labor Laws That Affect Labor Cost?
There are several construction labor laws that can directly impact your labor costs. Understanding them won’t only help you manage your expenses effectively but also ensure you remain compliant with legal requirements.
Here’s a closer look at some of these crucial laws:
- Minimum Wage – Construction workers are entitled to at least the minimum wage set by federal or state law. Minimum hourly wages per state can vary but for contractors working on covered federal contracts, the minimum wage for 2024 stands at $17.20 per hour according to Executive Order 14026. This is set to increase to $17.75 per hour on January 1, 2025.
- Overtime – As per the Fair Labor Standards Act (FLSA), non-exempt construction workers must be paid overtime for any hours worked beyond 40 hours a week. This overtime pay must be at least one and a half times the worker’s regular hourly rate.
- Breaks – In many states, employers must give workers a meal break, usually lasting 30 minutes to an hour, for shifts that reach a certain number of hours. However, whether this rule applies to construction workers can vary based on the state and the specific conditions of the job.
- Workers’ Compensation and Insurance – Workers’ compensation laws require construction employers to provide insurance for job-related injuries or illnesses, covering medical bills, lost wages, disability benefits, and rehabilitation. Employers must either purchase workers’ comp insurance or self-insure.
How Can You Legally Lower Construction Labor Costs?
There’s nothing wrong with trying to cut labor costs. What business wouldn’t want to improve efficiency and become more profitable – but it’s important that you do it legally. Here are some practical strategies that can help you get started in the right direction.
1. Conduct Better Cost Estimates
Cost estimation builds the foundation for creating your project budget.
If your initial estimates are off, it can lead to either over-allocating resources, which wastes money, or under-allocating, which can delay the project.
Now, unless this is your first project, you probably already have a rough idea of how much your labor costs are. To improve accuracy and avoid surprises, it’s important to take a more detailed approach:
- Use Past Projects as a Guide – Look at previous projects similar to the one you’re planning. This can give you a ballpark figure for labor costs based on what you’ve experienced before.
- Choose the Right Estimating Method – Different projects require different estimating methods. For instance, using a per-unit estimate (like cost per square foot) can work for large projects, while more detailed approaches like stick estimating, which breaks down every possible expense, are better for smaller projects.
- Factor in Labor Market Changes – Be sure to account for any changes in labor costs, such as wage increases or higher employee turnover. Adjusting for these factors will give you a more realistic picture of your labor expenses.
- Consider Contract Types – The type of contract you choose can also impact your cost estimates. In a time-and-materials contract, you bill based on actual labor hours, while a fixed-price contract sets a rigid budget for the project. Each has its pros and cons, but knowing which is best can help you stay within budget.
Don’t skimp on creating an accurate cost estimate. Accurate cost estimation helps prevent unnecessary spending and makes it easier for you to stick with your project budget.
2. Review Your Project Team Structure
Having the right people in the right positions on your crew can save you a whole lot of time and a whole lot of money.
Your team is likely a mix of skilled and general laborers so it’s important to assess whether the right individuals are leading the teams.
Sometimes, a highly skilled worker might not excel as a supervisor, which can lead to inefficiencies and increased costs. If a worker is better at their trade than managing others, consider offering further training or repositioning them to maximize their potential.
You also want to evaluate the workload distribution. Are your workers stretched too thin, or are their skills being underutilized?
To make the most of your workforce, consider implementing cross-training programs. This allows workers to learn new skills and take on different roles as needed. A more versatile team can adapt to changing project demands, reducing the need to hire additional staff for specialized tasks.
In some cases, using multi-skilled workers instead of relying on specialized labor can help streamline operations and cut administrative costs.
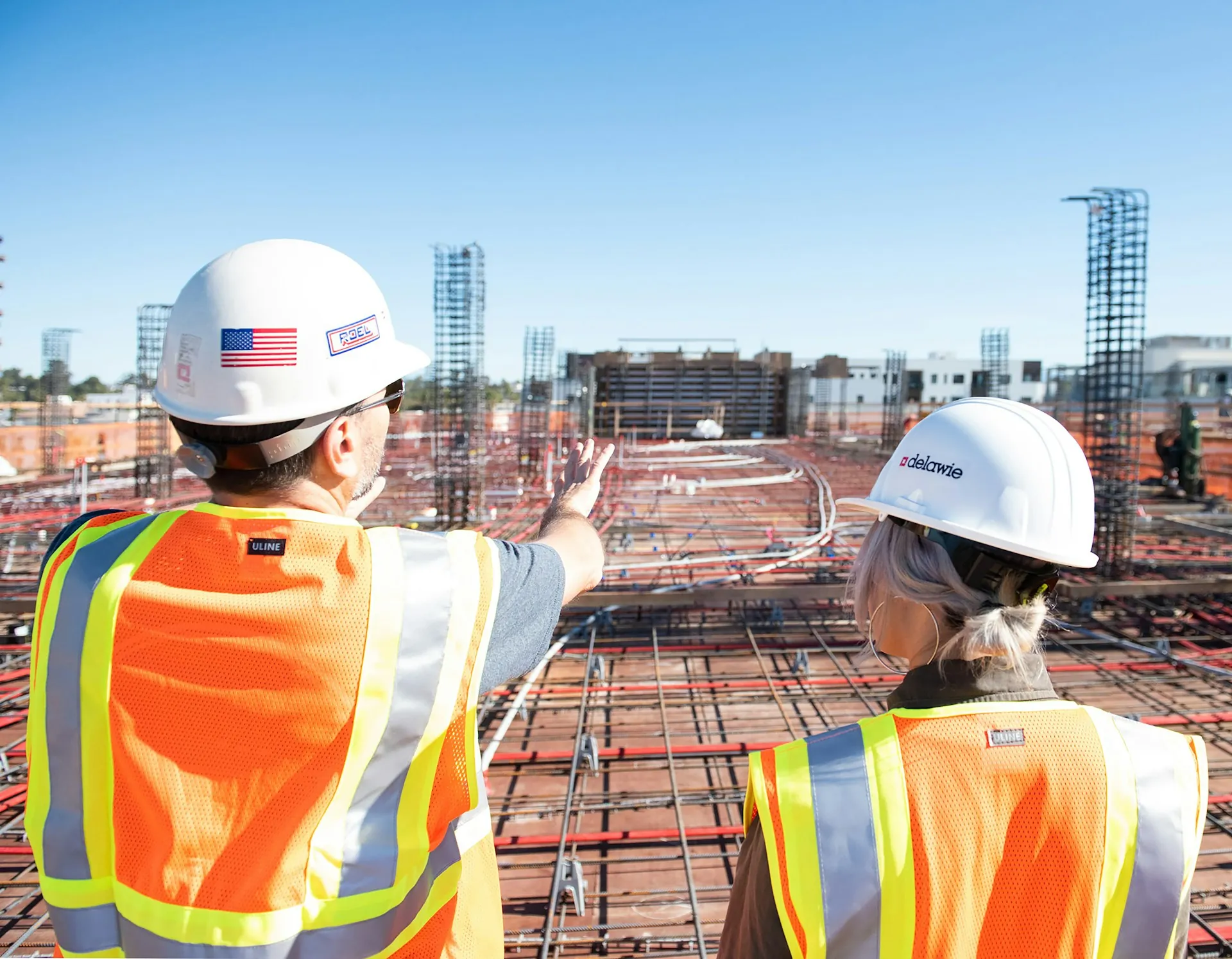
Photo by Joe Holland on Unsplash
3. Keep Accurate Track of Labor Hours
Given how construction workers are almost always paid by the hour, it’s important to know where those hours are going.
Some construction teams use manual timesheets to do this, but if you want to streamline the process, consider opting for construction time tracking software. These handy tools automate time tracking, so you won’t have to deal with the hassle of manual entries, which can lead to errors. Some time tracking tools even have facial recognition and GPS tracking features which can come pretty handy for multi-site construction time tracking.
Keeping detailed records of labor hours provides a clearer understanding of how time and resources are utilized. This not only helps in tracking actual labor costs but also aids in identifying areas where time may be wasted or misallocated.
Are some tasks taking longer than others? Are some employees logging more overtime than necessary?
By closely monitoring labor hours, companies can adjust schedules and workloads to stay within the allotted time, ultimately leading to significant labor cost savings.
Accurate time tracking also makes it easier to comply with labor laws and payroll requirements, minimizing the risk of disputes or penalties.
Learn more about how to effectively implement time tracking in construction.
4. Optimize Workforce Scheduling
Proper planning and scheduling of tasks are crucial for managing labor expenses and ensuring projects are completed on time.
To start, break down the project into smaller, manageable tasks. Each task should have a clear scope and timeline, allowing you to pinpoint which activities are essential for the project’s success. This approach helps you allocate resources more efficiently and reduces the likelihood of overscheduling employees.
By analyzing the tasks at hand, you can also identify non-essential activities that can be eliminated or postponed, leading to cost savings. This not only streamlines the workflow but also minimizes downtime, keeping your workforce productive.
5. Try to Reduce Turnover, But Also Don’t Keep on Dead Weight
High turnover can be expensive. This is true for almost any industry, including construction.
According to a study by the Center for American Progress, costs associated with replacing workers can range from 5.8% to even 213% of their annual pay. Note that this cost can vary significantly depending on several factors, including the employee’s role, the industry, and the specific skills required for the position.
To mitigate turnover, one of the most effective strategies is creating a more supportive and rewarding work environment. Offering competitive benefits, such as paid time off (PTO), health coverage, and performance-based bonuses, can go a long way in retaining your valuable employees.
These benefits may incur upfront costs but they serve as long-term investments by boosting employee satisfaction and loyalty. And they can definitely save you on labor costs over time.
Now, while reducing turnover is crucial to cutting labor costs, holding on to workers who aren’t pulling their weight can be just as expensive, if not more. Unproductive employees can affect team dynamics, slow down project timelines, and lead to additional costs, whether it’s through overtime for other workers or redoing poorly executed tasks.
That’s why it’s essential to assess your workforce regularly. Offer struggling employees opportunities to improve through coaching, clear communication, and setting specific performance goals. If improvement isn’t seen after reasonable efforts, it may be time to make the tough call and let them go. Holding onto “dead weight” in the hopes that things will change can end up being far more expensive in the long run.
It’s all about finding a balance between investing in your workforce and making strategic decisions for the overall health of your business.
To Wrap Up
Construction is a highly competitive industry. It’s definitely not for the faint of heart. To succeed requires a good understanding of not just the building process but also the intricacies of managing labor costs and compliance with regulations.
Hopefully, these strategies have provided you with valuable insights into optimizing your labor costs so you can be better positioned to navigate the complexities of the industry and lay the foundation for long-term success. Cheers!